PROFILE
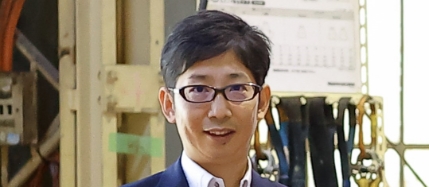
2003年入社
自然環境科学科 卒業
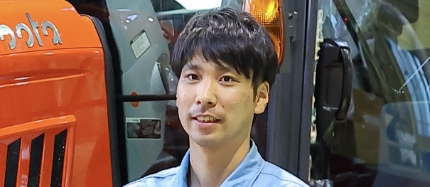
2012年入社
知的力学システム工学専攻 修了
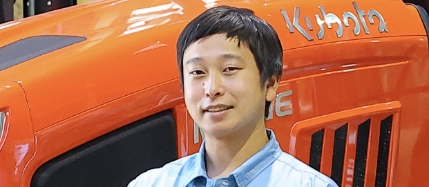
2014年入社
総合機械工学専攻 修了
トラクタニューモデル
“GENEST”の開発裏話
※GENEST:畑作や酪農・畜産の作業で活躍する最大135馬力のトラクタ
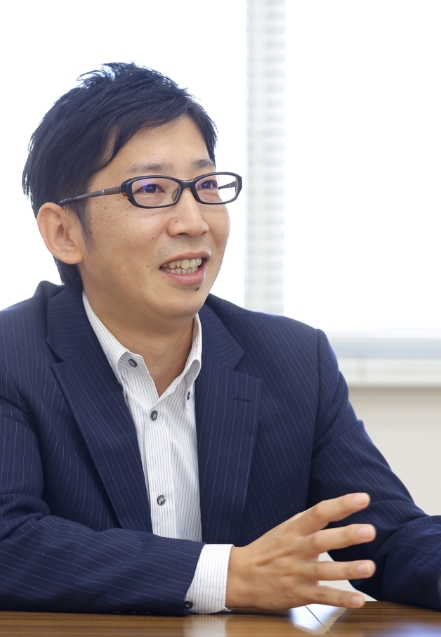
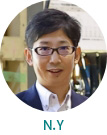
Tさんとお会いするのは、2017年発売のトラクタ “GENEST”の開発で協力し合って以来ですね。
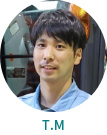
その節はお疲れさまでした。Nさんは「GENEST」の製品開発企画から市場導入まで幅広くご活躍でしたね。販売会社の営業要望の整理に始まり、生産販売台数の調整や、販促手段を含めた市場展開策の立案・展開など、多方面で尽力されて大変な様子だったと伺っています。
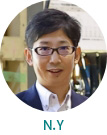
トラクタ新機種を市場導入する際はいつもの仕事なので、もう慣れてきましたけど。GENESTの場合はあえて言えば、排ガス規制に対応する装置を付加しないといけなかったことに少々苦労したかもしれません。地球環境を考えると必要ですが、農作業そのものには直接関係しない装置なので、それを付けていかに農家のお客様の納得を得るコストパフォーマンスをアピールできるかは大きな課題でしたから。GENESTに搭載する部品や製品の性能評価を手掛けていただいたTさんには、とても頑張っていただいて感謝しています。
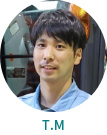
市場要望に応えるために燃料タンクの形状を変えたり、バッテリーを国産のものに変更したりといった部分をいくつか担当しましたが、もちろん私一人でGENESTの製品評価をすべて担えたわけではありません。同じ部門の他のメンバーをはじめ、常に設計部門やNさんが所属している製造部門などと一緒にコンカレント(同時進行技術活動)を実施しました。そのおかげで、製品企画通りに高品質な機械を形にできた一つの成果だと思います。そうですよね、Nさん?
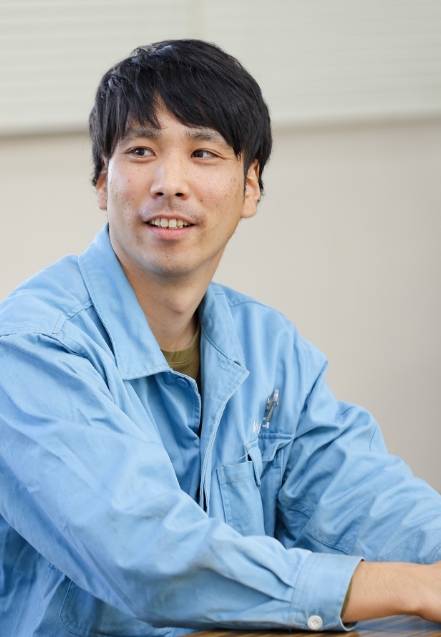
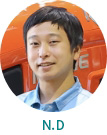
私はGENESTの開発には携わりませんでしたけど、製造部門も普段から品質確保に向けて関連部門と密に協同しています。例えば新機種の試作機の製作ではどのような構造にするのが最適かを技術部門と一緒に考え、双方で問題点を洗い出しながら生産に必要な設備、工具、ジグなどを整えていったり。生産ラインにふんだんに予算を投入してまったく新しい作り方をするなら話は別ですけど、製造コストを抑えるために既存の生産設備類をできるだけ活かしていくモノづくりはなかなか難しいですからね。GENESTは洗練されたデザインの新機種なのに、開発ベースはコスト制限がかかる前機種のマイナーチェンジだったと聞いたので、各開発部門でさまざまな苦労があったことは十分に想像がつきます。
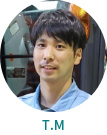
確かにGENESTでは新デザインのボンネットを作る際、安定した組み立てができないということで製造部門から指摘が入り、設計から見直したところもありました。開発フローに沿って設計、製品評価、製造と一直線に進められればよいのですが、各部門で問題を発見するたびに流れが行ったり来たりするのが新機種開発の難しいところです。
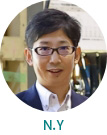
私の担当範囲だったGENESTのネーミングについても、使える商標の選択から決定に至るまでは行ったり来たり、何度もやり直しました。きっと開発に関わるそれぞれの部門が発揮する真摯なこだわりとやり取りが、市場から確かな支持を受けるクボタ製品を生み出しているんでしょうね。
日々の仕事に感じる
それぞれのやりがいは
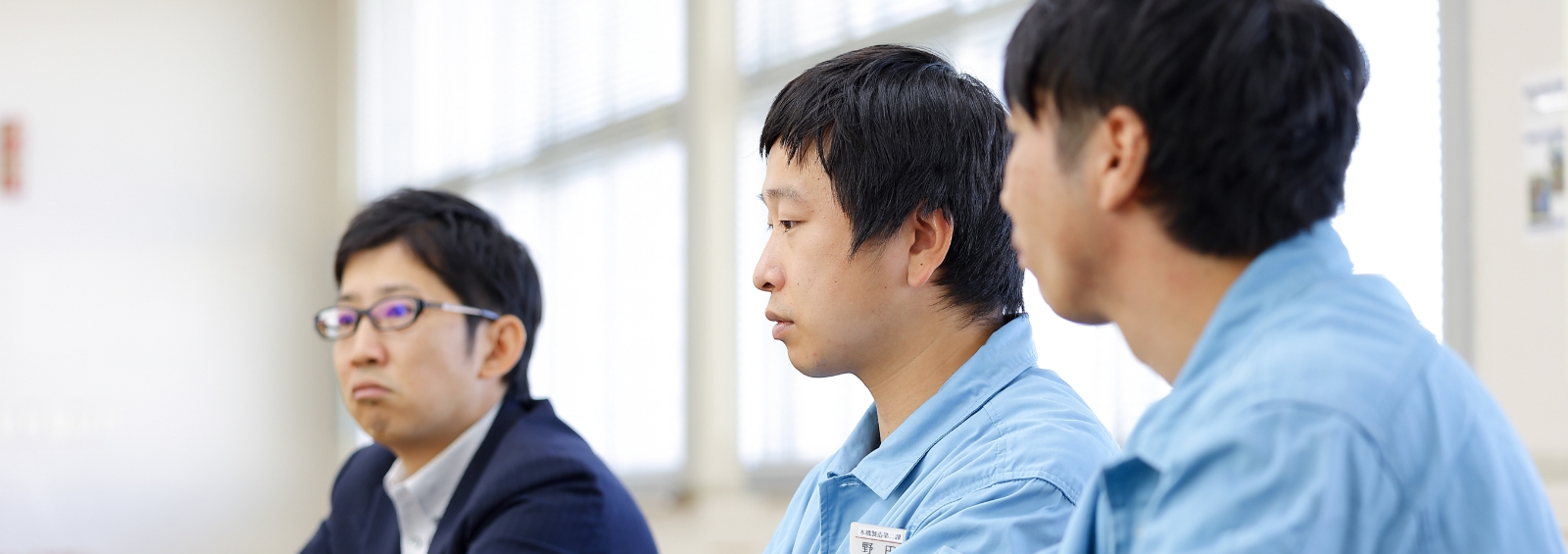
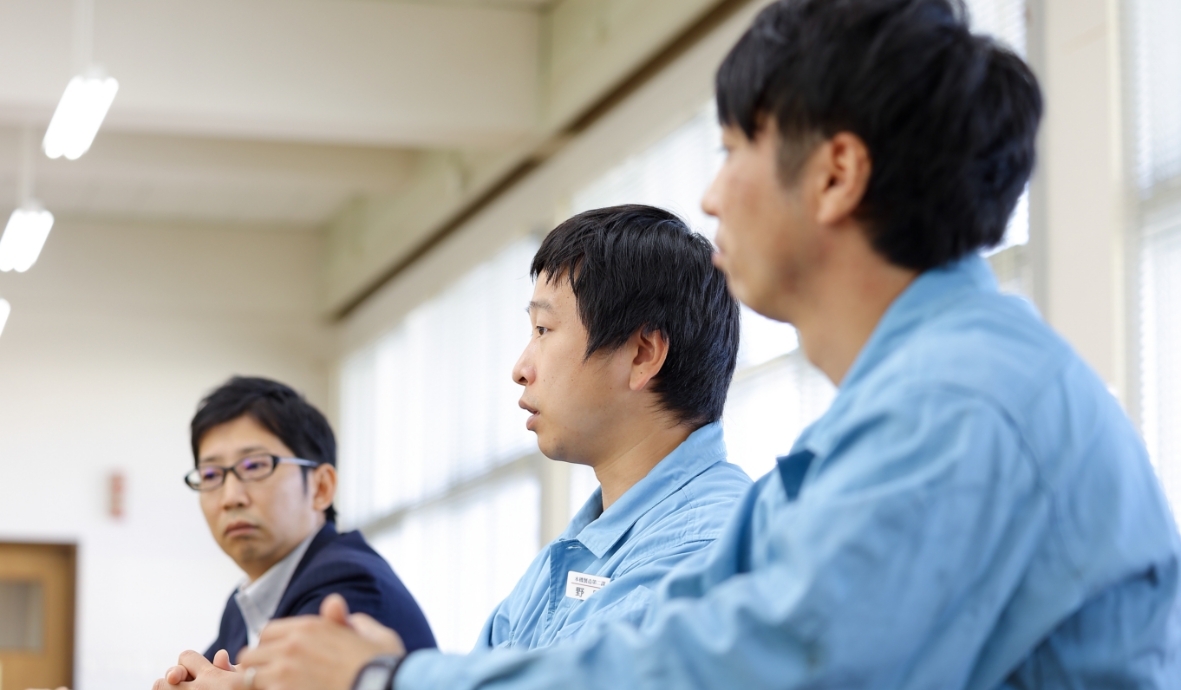
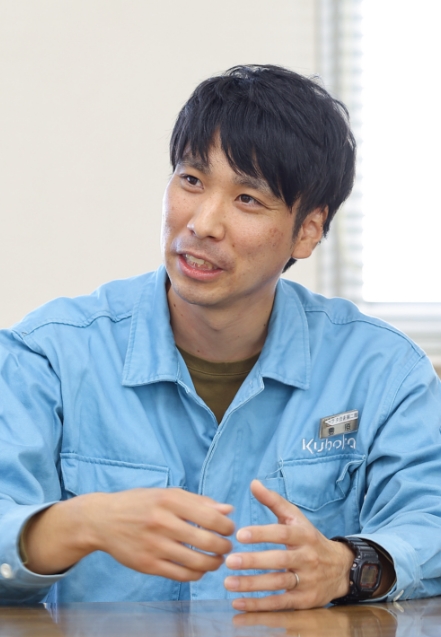
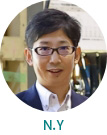
お二人は仕事で日頃、どんなことに気をつけていますか? 私は営業担当としてQCD(品質・コスト・納期)をベースにしたさまざまな条件にどう優先順位を付けて市場導入するのが最適か、社内外の調整を含めて考え尽くすことに注力しているんですが。
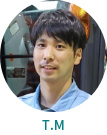
私はお客様の満足を得られる製品を作りたい思いが根本にあるので、仕事では品質面の確保を特別に意識します。仰るようなQCDのバランスの折り合いをつけつつ、的確な評価を通じていかによりよい品質のものを作り上げられるかを追究しています。
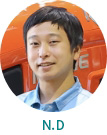
現在トラクタ新機種の生産準備を担当している私も、製造品質の確保が第一ですね。特に、製品不良を出さずコスト削減も実現するために、作業する現場スタッフが組み付けしやすい構造を考えて開発に活かすことを強く意識しています。
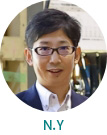
仕事のやりがいの面はどんな風に感じているんでしょうか?
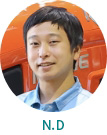
新しい技術を応用することで今までできなかったことをできるようにしたり、仕事を効率化できたりするとやりがいを感じます。最近、製造上の問題点のリストアップとその後の対応について関係メンバー間で共有しやすいようタブレット端末を利用することを提案したんですが、これが案外上手くいって解決へのプロセスが明瞭でスピーディーになり、非常に達成感がありました。
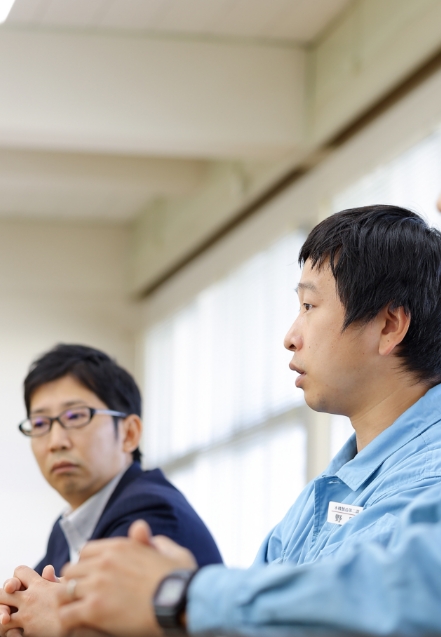
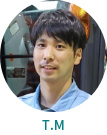
私は自分が関わった製品について、お客様や販売会社から好評を得たと聞いたときが一番のやりがいです。加えて、トラクタ全体に関する製品評価をチーム一丸で推進していることにも魅力を感じています。Nさんはいかがですか?
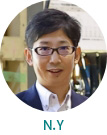
製品開発のスタートから量産、発売、さらにディーラーさんの販売活動まですべてのフェーズに携われるのが営業のやりがいであり、醍醐味ですね。それだけ広範囲に目を配る必要があるので、プレッシャーは半端なものではないんですが(苦笑)。お二人も仕事でプレッシャーを感じるときがあるのでは?
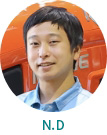
製造現場にトラブルが起きた時はかなり焦りますね。生産を止めるわけにはいかないので、素早く解決するために携帯電話で現場と何度もやり取りして、あっという間に電池が半分になったこともあります。
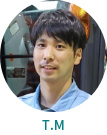
製品開発でもトラブルはつきもので、対応に頭を悩ませる場面は多いんです。そういう意味ではプレッシャーを日常的に当たり前に受け入れる状態になっているかも(笑)。
クボタのモノづくりと
会社について思うこと
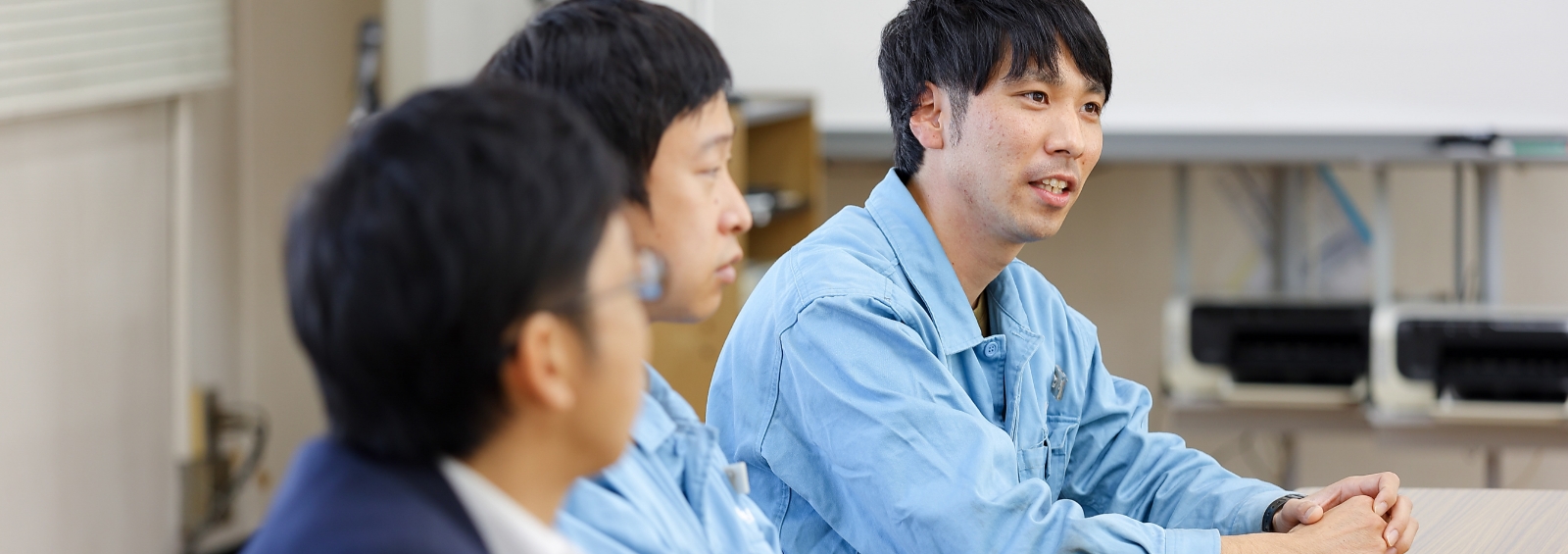
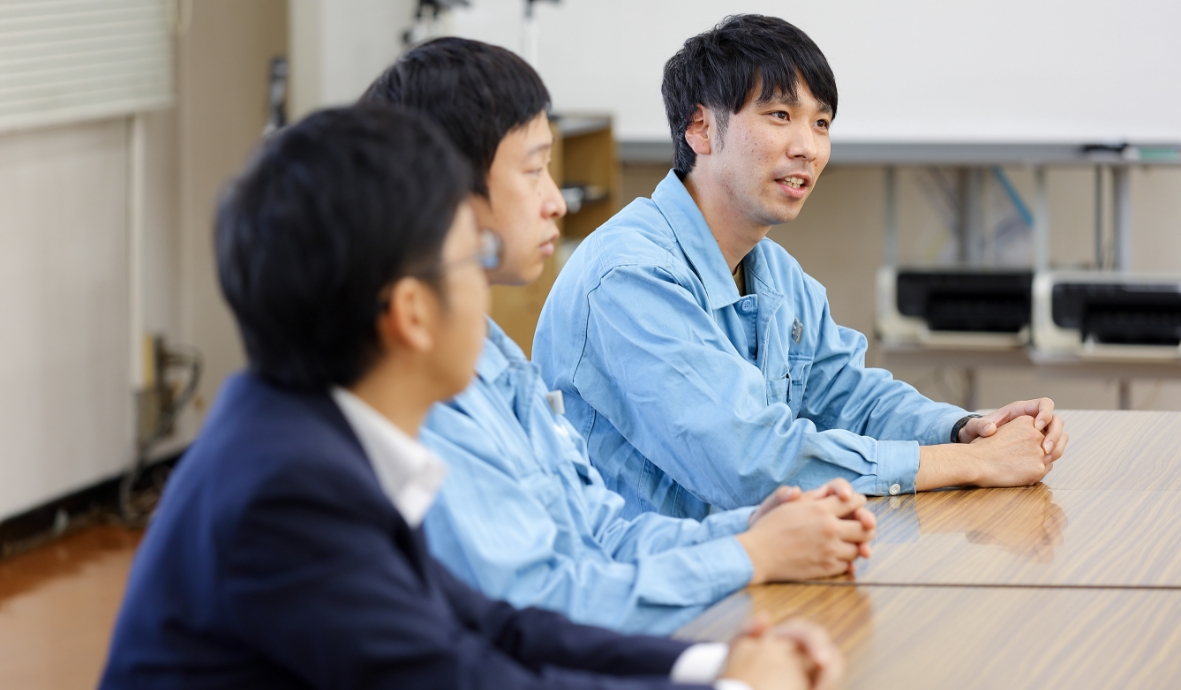
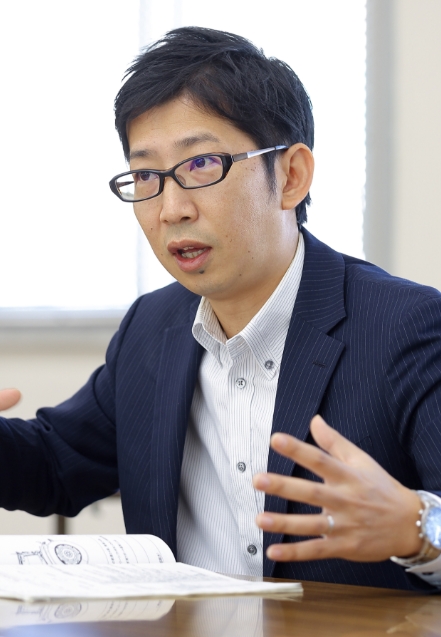
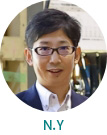
私がクボタに入社してからもう18年目。クボタが作り続けてきた豊富な製品ラインアップとその品質の素晴らしさを、多くの販売会社やお客様と接する中で実感してきました。開発メンバーとして、クボタがそうした製品群を実現できるポイントについてどう考えますか?
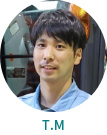
製品開発の仕事は一人で作業することが少ないせいで思うのですが、ひと言でいうと「チームプレイ」ではないでしょうか。限られた時間と人員の中で苦しい開発局面も次々とやってきますけど、チームメンバー同士の結束がすごく強固だから乗り切れていると思っています。
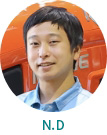
堺製造所ではさまざまなトラクタを多品種少量生産で製造しており、一人の作業スタッフが一機種の組み立て方を覚えたり、組み立てるのにどうしてもある程度の時間が必要です。その中で生産の効率化を図るために、常にいろいろな部品や設備、システムに「工夫を加える」ことで優れた製品群を製造できているのだと思います。
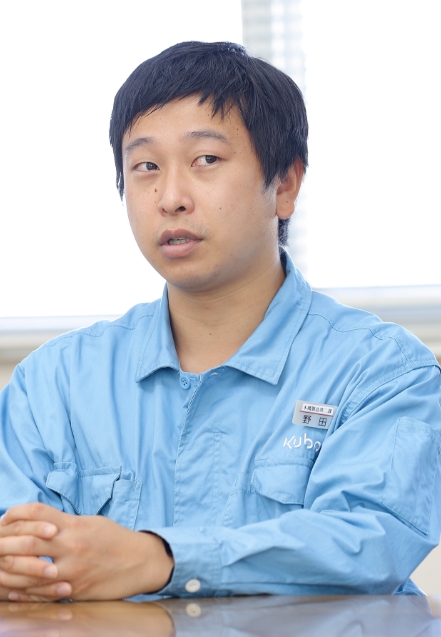
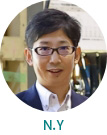
そうして皆さんが進化させている製品群を迅速に市場に普及させる、たくさんの販売会社や営業所、そして販売第一線に多くの素晴らしいセールス・サービススタッフの方々が居て下さるのもクボタならではの特徴。「グループ力」もクボタのモノづくりや会社の強みだと思います。
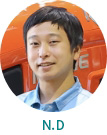
そこに伸び伸びと楽しく仕事ができる社風も加えたいところです。製造に関わるメンバーは皆温厚で人柄がよく、オープンに話し合える方々ばかりですから。
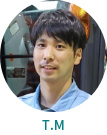
開発部門には総じてそのような人柄の方が多いですよね。
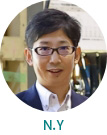
同感です。私もこれまで困ったときには必ず周りに手を差し伸べて助けてくれる人がいて、心強く仕事をして来られましたしね。これがクボタの魅力のひとつだと思います。