PEOPLE
GROUNDBREAKERS日本農業の未来へクボタ堺製造所見学!モノづくりの「改善」に迫る【前編】
2022 . 07 . 29 / Fri
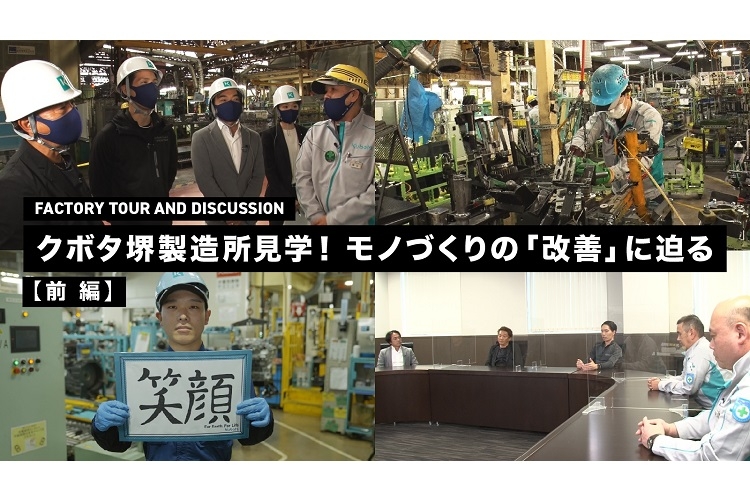
写真・文:クボタプレス編集部
2021年に開催された新春オンラインイベント「GROUNDBREAKERS」で紹介された3人の農業経営者がクボタの堺製造所に潜入!前編ではまず、普段なかなか見ることができないエンジンやトラクタの生産ラインの様子を見学し、モノづくりの「改善」にどのように取り組んでいるのかを探ります。
クボタのマザー工場を作物づくりのプロが偵察
今回、工場見学に参加されたのは、徳島県で青ネギ栽培に取り組む酒井貴弘さん、愛知県で200ha以上を耕作し、米、麦、大豆の栽培に取り組む高村昭広さん、宮城でうるち米ともち米、大豆、ネギの栽培に取り組む村上和之さんのお三方。
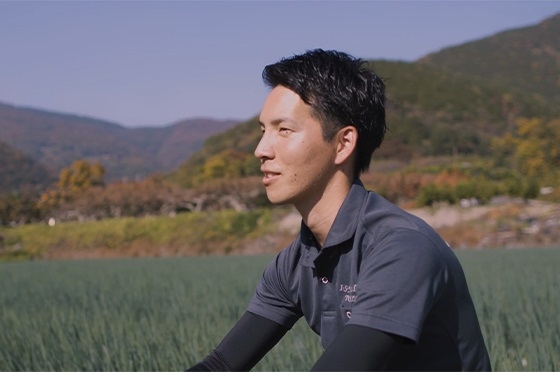
アイ・エス・フーズ徳島株式会社代表取締役の酒井貴弘(さかい たかひろ)さん。
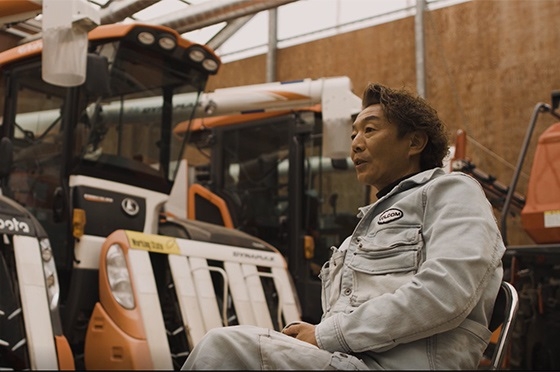
株式会社アグリ知立代表取締役社長の高村昭広(たかむら あきひろ)さん。
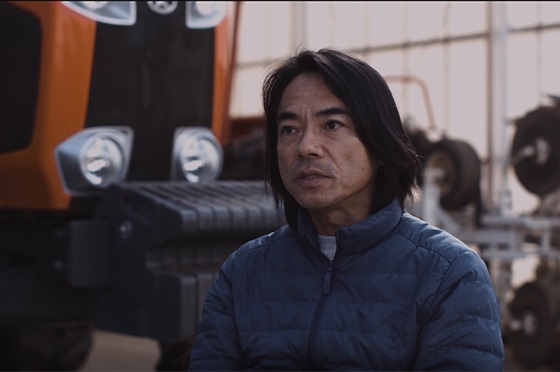
農業組合法人 野菜のキセキ理事の村上和之(むらかみ かずゆき)さん。
見学先の堺製造所は1937年(昭和12年)に操業を開始。自動車会社以外では国内民間企業初のベルトコンベアーシステムを採用した歴史ある工場で、年間約3万7,000台ものトラクタを生産し、世界各国へ輸出しています。生産部門だけでなく研究開発部門もあり、国内外に向けた農業機械・建設機械・エンジンなどの製品開発、技術開発を行っています。
堺製造所ではKPS(Kubota Production System=クボタ生産方式)に基づき、よりよい商品をスピーディにお客様にお届けするため、日々改善に取り組んでいます。ここでは、その一部を紹介します。
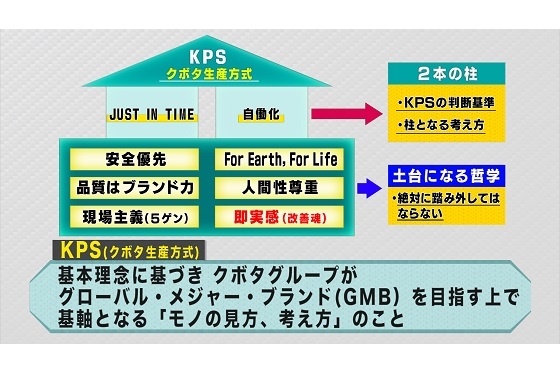
KPS(クボタ生産方式)の基本理念は、「お客様の望みを超える商品とサービスを、予測を超えるスピードで提供することにより、感動を呼ぶモノづくりをめざす」こと。原材料調達から生産管理、物流・販売までの過程において、作業の無駄を徹底的に排除。
100年の結晶 エンジンライン
まず、最初に見学するのはエンジンの製造工程です。この組立ラインでは、①振り向かない、②歩かない、③手元化(手元で組み立てる)、④誰がやっても同じ作業ができる仕組みをつくる、という4つのコンセプトでラインを構築しています。
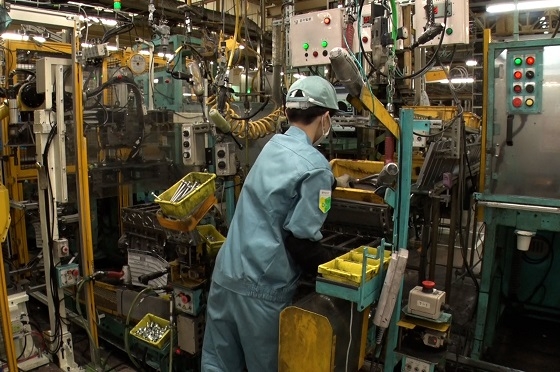
部品はすべて前方から供給され、作業ツールも40cm以内に配置。振り向かず、歩かず、手元で組立が可能。
また、工場内の床のラインに沿って移動中の装置はAGVという無人搬送車で、運搬する人のムダをなくすために導入しているそうです。
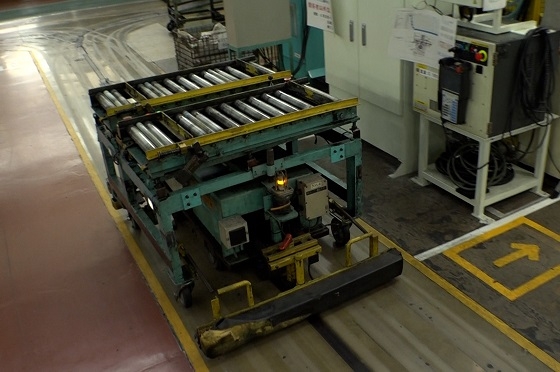
AGV(無人搬送車)。床に埋め込まれている誘導路をもとに、さまざまな部品などを運びます。
案内役の職長が入社まもない作業員の様子を見ながら、ひととおり作業ができるようになっても、しゃがんで作業しているのでは効率が悪い、これも「改善」を検討するポイントだと指摘。「単純作業をしているなかで、どうやって社員のモチベーションを保っているんですか?」という質問には、常日ごろからもっと改善できるところはないかを作業員自らが意識し、簡単な改善は自主的に行うことで本人のやりがいにつながっていると答えます。
次に、クボタが力を入れる「ポカヨケ装置」。ポケヨケとはポカ(作業ミス)をよける(避ける)という意味で、ミスをなくす改善ポイントです。例えば、ボルトを完全に締め切らないと工具が元に戻らないため、締め忘れや中途半端なトルク不足の防止につながります。村上さんは「だから、間違いが起きないんですね」と感心。しかし、それでも間違いは常に起こりうるため、ポカヨケや自働化に頼りすぎて人間の能力が衰えないように注視していく必要があるようです。
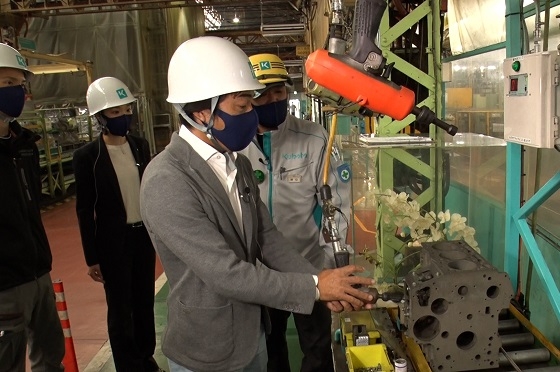
ポカとは作業ミスをさし、もともと囲碁や将棋の言葉で、考えられないくらいの悪い手を打つことを表します。
その説明を聞いていた酒井さんが「クボタさんの『改善』の最終形とは、どんな形をめざしているのか」と疑問を投げかけると、職長からはこのような答えが返ってきました。
「改善に終わりはないと私は思っています。人が関わる限り、改善の余地は無限にあります」
「まるで映画の世界」ミッションライン
次に見学したのは、トランスミッション*1のピッキング*2工程。型式ごとに部品が異なるので、正確さが求められます。
- *1.トランスミッションとはエンジンなどの動力を走行や作業に適した回転に可変させる装置。
- *2.必要な部品をピックアップして集める作業。
ここで採用しているのは「ランプピッキング」というシステム。各部品が入った箱の下にランプとデジタル表示窓があり、ランプが付いた箱から、表示された個数の部品を取っていく仕組みです。以前は部品を集めるだけでしたが、集めた後に組み立てると部品に2度触ることになるため、今はピッキングしながら、その場で部品の一部を組み立てているそうです。また、作業はAGVに乗ったまま行われます。以前は歩きながら作業をしていましたが、「歩行数が増えるのは最大のムダで、いかに疲れずに作業できるかがいい仕事につながると考えたからです」と案内役の職長は言います。
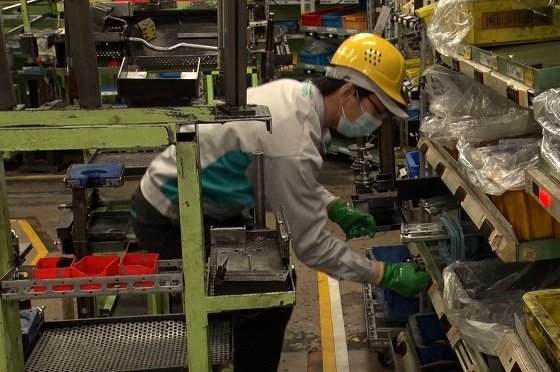
「ランプピッキング」と呼ばれるシステム。先にランプを消すとどの部品をピッキングするかわからなくなるので、ランプが点灯した箱の部品を取ってから消すことを徹底しています。
集めた部品を使った組み立て工程のスペースでは、プロセスに応じて必要な工具が上から順に降りてくる仕組み。さらに、無理なく自然な動作で作業できる範囲を「ストライクゾーン」と呼び、常にその範囲内で作業をすることで動作のムダが省けるよう、工夫しているそうです。「次々、勝手に降りてくる」と感心する高村さん。この形に行き着くまでに2年かかったという説明に、お三方から一斉に驚きの声が上がり、「映画の世界ですね」という感想も飛び出しました。
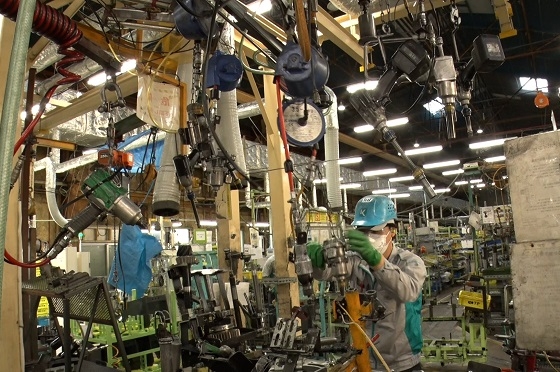
必要な工具が必要な時に上から降りてくるシステム。しゃがむ、歩く、手を伸ばす、探すという4つの動作のムダが改善されています。
コラム 私の身近な「こころがけ」
次の工程見学に進む前に、ここでちょっと閑話休題。堺製造所で働く若手3人に、毎日仕事をするうえでどんなことを心がけているかを聞きました。
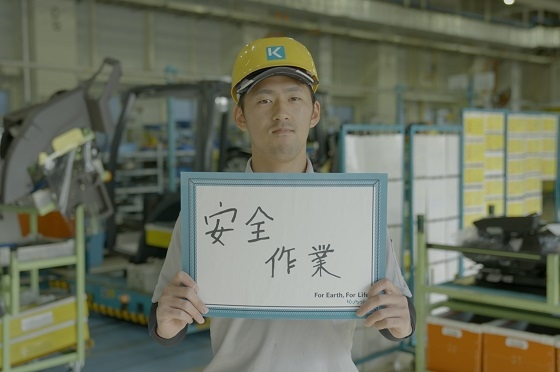
堺本機製造部 本機製造第二課の谷口翔(たにぐち しょう)さんのこころがけは「安全作業」。自身が怪我をするとラインがストップし、トラクタを待っているお客様に届かなくなるため、作業前に危険予知をしたうえで、細かい作業も意識して行っていると語ります。
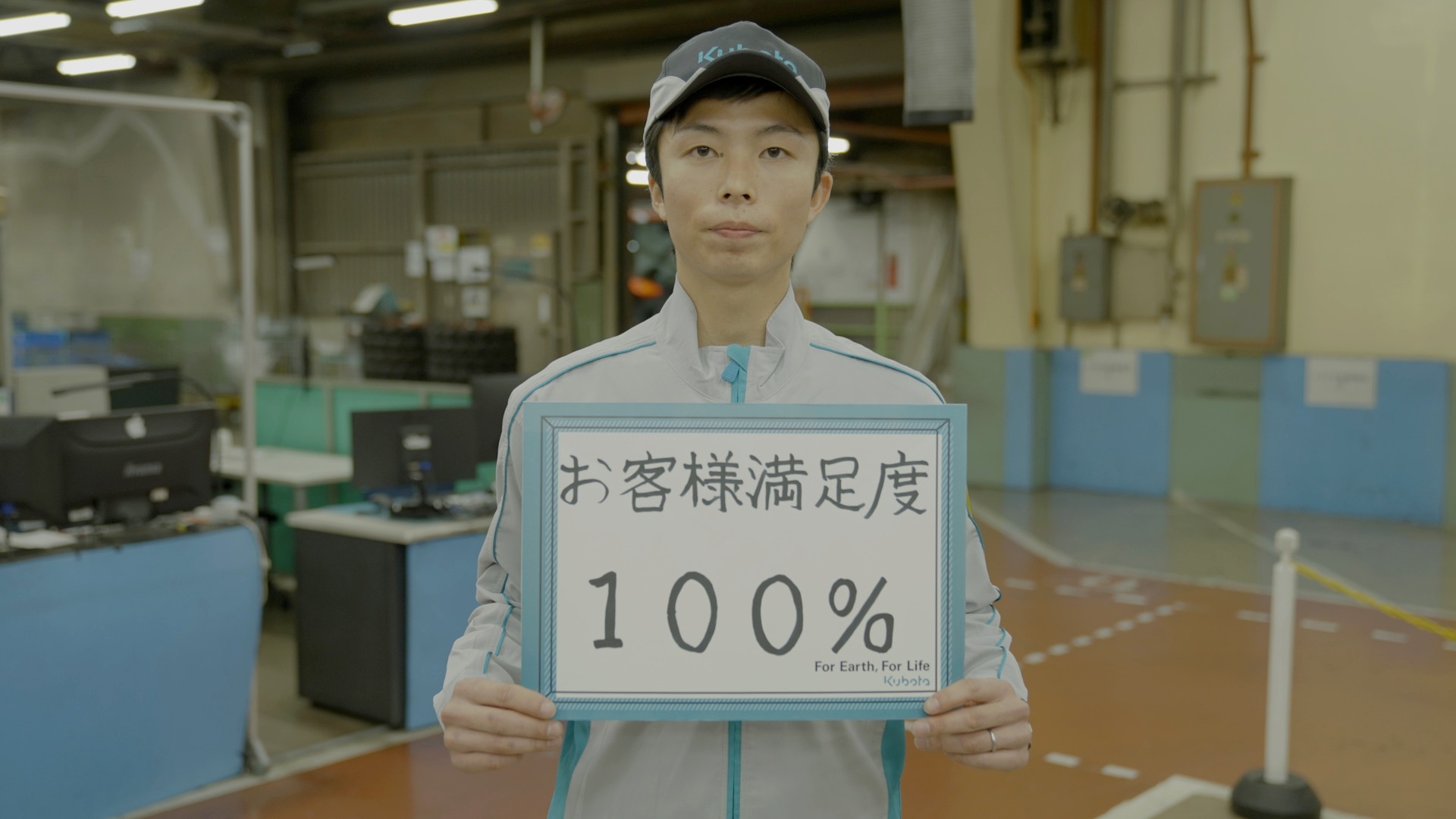
堺本機製造部 本機製造一課の貴嶋倫規(きじま とものり)さんのこころがけは「お客様満足度100%」。農業に従事する父の「クボタのトラクタがないと仕事にならない」という言葉を聞いて、待ち望むお客様に感動を与える確かな品質の製品をつくりたいと思うようになったそうです。
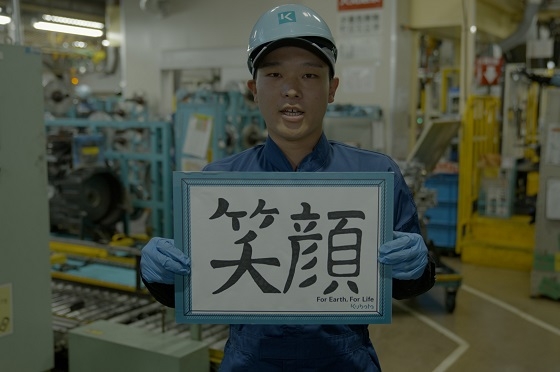
堺エンジン製造部 組立課の清川広人(きよかわ ひろと)さんのこころがけは「笑顔」。作業に支障が出た作業員のサポートを引き受けるリリーフマンを務める清川さんは、「お客様はもちろん、各作業担当者など、クボタにかかわる一人でも多くの人に笑顔になってもらいたい」と言います。
座りながら効率化 キャビンライン
さて、続いて見学したのは、トラクタの運転席であるキャビンの組み立てライン。ここでは「岡持ち」と呼ぶ工具箱に工具をまとめ、部品も整列させて揃えておくことで効率化を図っています。また、流れ作業ではなく、1台のキャビンの組み立てを1人の作業者が集中して行っているのも特徴です。必要なものを、必要なときに、必要な数だけつくる「JIT(Just In Time)」の考え方をさらに一歩進め、「必要な姿勢、必要な順番で」を加えた「新JIT」をめざしています。
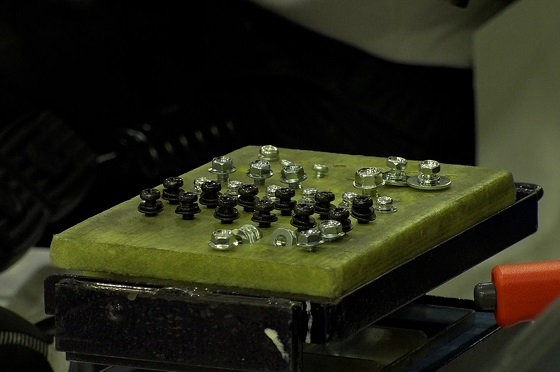
部品を見やすいように整列させて、探す動作のムダを省いています。
ついに完成 艤装(ぎそう)ライン
最後はトランスミッションとキャビンをドッキングさせ、大型トラクタを完成させる工程です。
職長の説明を受けていると、頭上で何か大きな物体が動いていることを察知したお三方。見上げて注目していると、キャビンが降りてきました。全員、興味津々です。
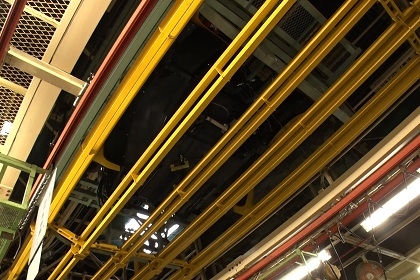
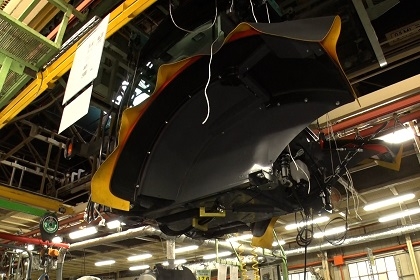
ゴンドラに積まれたキャビン。黄色い柵が横にスライドし(左)、ゆっくりと降下。下から見ると予想以上の大きさです(右)。
その後、上のキャビンと下のトランスミッションの配線などを接続する作業を経て、ついに合体。最後に、馬力を測定するなど、さまざまな検査工程を経て、安全が確認されれば無事出荷され、農家の皆様に届けられます。
次回の後編では、GROUNDBREAKERSのお三方に2人の職長も交えて、製造所見学で感じたことや学んだこと、さらには農業への応用などについて、トークセッションを行います。