TECHNOLOGY
人とモノが共生・協働するスマートファクトリー《進化する阪神工場》ロボット導入で鋳造の現場はこう変わった!
2018 . 01 . 31 / Wed
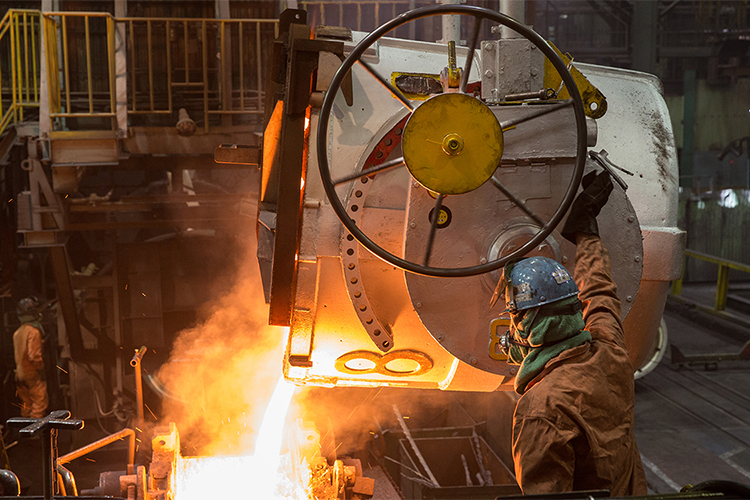
文・写真=クボタプレス編集部
ICT(情報通信技術)やIoT(モノのインターネット)の活用は、今日世界的に、多様な産業分野で広がりを見せています。日本の製造業も例に漏れず、プラントや生産ラインの遠隔監視・不具合の未然防止などの形で採り入れるようになりました。施設内にネットワーク/センサを設置して得たデータを解析し、操業状況を可視化。それにより人員配置の最適化、製品歩留まりの向上、技術の標準化などのメリットが見込まれます。
概して、センシング技術と密接に関連するFA機器といえば、人と共に働く産業用ロボット。かつては自動車産業をイメージするものでしたが、近年、非自動車産業からも期待とニーズが高まってきました。背景には作業効率化のほか、人件費や技術者の世代交代に対応する少人化などの課題があります。
時代の求めるソリューションを生み出すクボタは、生産環境と働き方改善にも注力しています。“スマートファクトリー”となった阪神工場の武庫川事業所を訪ねました。
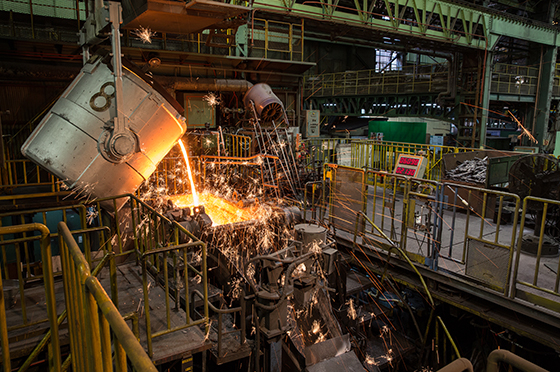
小管鋳造の注湯作業風景(リニューアル後)。リモート操作でロボットが傾動作業を行うようになり、人と溶湯(ようとう)・取鍋(とりべ)との接触リスクが解消されました。
鋳造のIoT活用は難しい?
鋳鉄管の専門工場として1940年に設立された阪神工場(武庫川事業所)は、水道管路工事に使用されるダクタイル鉄管を中心に、国内向けの用途や工法に応じた鋳物製品の製造を担い、クボタのモノづくりを支えています。世界で加速するIoT活用の動きを受け、クボタもKSAS[農業機械とICTを融合させたサービス]やKSIS[水環境インフラ分野におけるIoTサービス]を手掛けるなか、2016年に入って、前例の少ない鋳造分野で工場のシステム化を検討。ロボットを生産ラインに導入する試験を経て、約半年後に現場のリニューアルが実現しました。
ダクタイル鋳鉄は開発当時(1948年米国)、“第三の鉄”といわれ、あたかも今世紀最大の発明のような勢いで業界を席捲しましたが、製造は極めて難しく、実製品への応用は至難の技でした。10年近い試行錯誤の末に、クボタが遠心力鋳造法によるダクタイル鋳鉄管の量産を実現させた歴史があります。今日、IoTへの取り組みは各産業で進んでいますが、この分野ではあまり聞かないようです。試みが多くないのは、やはり難しいということでしょうか。
「小管(口径75mm~250mmの水道用鋳鉄管)の生産ラインをリニューアルして、約1年半になります。後ほどご説明するように、鋳造のIoTはセンシング技術の関係で非常に難しく、私たちのねらいは完全自動化ではありません。人に替わってロボットが行う工程と、人が価値を担保する工程があり、その住み分けによって品質向上やコストダウンなどの目的を達成します」(生産技術課 西原幸祐さん)。
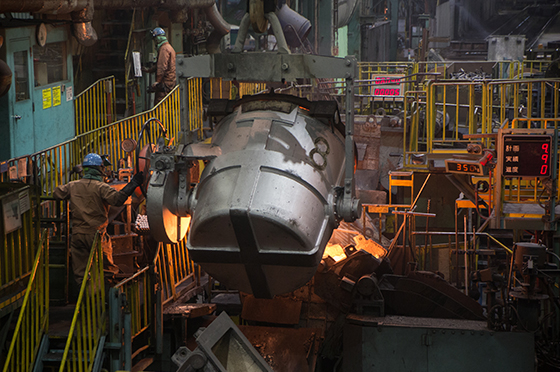
ロボットが人に取って代わるのではなく、人とロボットが協働することによって、技術の標準化・品質向上を実現。延いてはコストダウンなどのメリットにつながります。
技術の標準化で安定の高品質に
日本の鋳造業界を牽引してきたクボタには、長年蓄積してきた高度な技術とノウハウがあり、手作業で到達不可能なレベルと生産量に引き上げるためのオートメーションとは、意味合いが異なります。
「暑熱・粉塵を伴う環境での安全面配慮と技術の標準化が最たる目的です。ロボットの作業ペースは人と同等に設定しているため、生産する本数は変わりません。しかし、1本あたりのピッチが揃うことから、個人差のない均一な品質を常に確保できます。ロボットのパフォーマンスがそれほど精緻であっても、仕上げの工程は手作業なのです。ベテランの技術者がどれほど優れているか、お分かりになりますね。
安全確認も人の目で行います。プロの目視はとても的確で、溶鉄の赤みや火花の飛び方などで適正な温度や異変を察知します。センサの感度は高まっていますが、ベテランの体感値までの高精度化は難しいと思われます。また、見ることに加えて重要な『判断』は、特に非常時、人にしかできない部分です。今後も人とロボットが生産ラインで協働を続けます」(西原さん)。
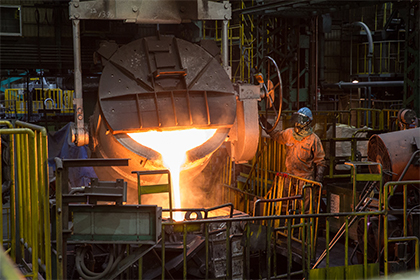
定置取鍋を傾動させ、三角取鍋内に目標レベルまで溶湯を供給。
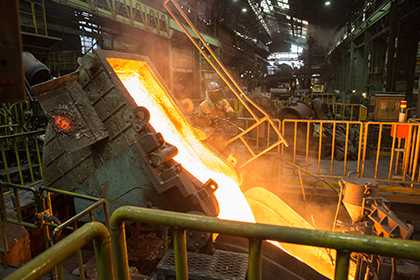
三角取鍋から注がれた溶湯はシュートを介して、高速で回転する型に流し込まれます。
少人化がもたらすメリットと技術の継承
生産プロセスの一部をロボットが巻き取ることで、人員や設備の配置は変わります。小管鋳造には、アカ掻き・ジャミ取り・シュート塗型といった工程があり、最も機械化は高難度とされるアカ掻きも含め、ロボットの鋳造機操作に成功。従来の7名程度から5名にチーム編成を変え、工場内のラインとネットワークを清流化しました。より安全かつコンパクトな設備で、少人数/一定生産量/高品質が実現し、大きなコストダウンが期待されています。
「若手の技術者が各工程を経験し、一通りの技術を培って、鋳造のスペシャリストになるには年月を要するものでした。経験豊富な技術者が負荷の高い工程や仕上げ作業に固定従事してきましたが、標準化後は熟練者でなくとも作業可能です。これからは、『手作業の習熟』よりもIoT環境下での『リモート操作や見きわめ』に重きが置かれるため、現場戦力の育成や業務の引継ぎはしやすくなるでしょう。人選やレイアウトの自由度が広がります。
一方で、懸念事項もあります。3年に一度くらいしか起こり得ないレアケースに関しては、マニュアルで網羅し切れないので、発生ベースで熟練者を中心に臨機応変な対処をして、ノウハウを共有し、スキルや専門知識を継承していきます」(西原さん)。

赤枠内がロボット。湯面をカメラで監視しながら、操作室から遠隔操作します(矢印が示すのは、シュート塗型を行うブラシ)。
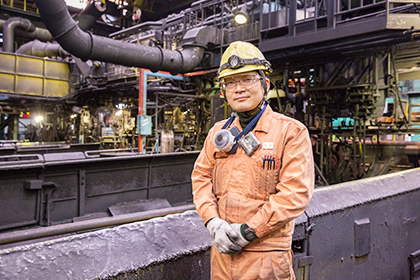
小管ラインのリニューアルについてお聞きした、生産技術課 西原幸祐さん。
徹底的なムダ排除を目指すスマートファクトリー
阪神工場のIoT化は、ロボットを導入した生産活動によるメリット創出と併行し、もうひとつのパートから構成されています。最後に、蓄積データの解析に基づく業務改善(ムダの排除)について、KPS推進課の足立誠さんに伺いました。
「約3年前から “工場の見える化”、つまり、施設内ネットワークから収集したビッグデータを解析して、操業の傾向や設備の状態を数字やグラフに表しています。その分析結果をもとに、計画と指標に即した効率的なパフォーマンスを目指すべく、人・モノの制御が行われます。
例えば、工場で使用するガスや電気などのエネルギー。昨今、全世界で環境規制と省エネルギーが意識されていますね。具体的な施策を立てて、工場全体のCO2量などの削減を達成するには、『運転時間中』に『どのライン/設備』で『どれだけ』消費あるいは排出しているかを把握することが必要です。そのようなアプローチで、作業者の動きや生産の進捗、材料・機器の状態についても計測し、多角的な課題解決に結びつけます。
ロボットの導入によって省人化が実現した分の人材には、製品開発やビッグデータ解析・モニタリングといった他の業務への注力が期待されます。これらは費用対効果や高付加価値の創成に関係し得る、IoT時代らしいポジションともいえます」
生活に欠かせないライフラインである水道インフラを構築するダクタイル鉄管の供給拠点として、クボタのモノづくりを支える阪神工場では、大管と中管の部門でもリニューアルが進行中です。さらなる進化に引き続きご注目ください。
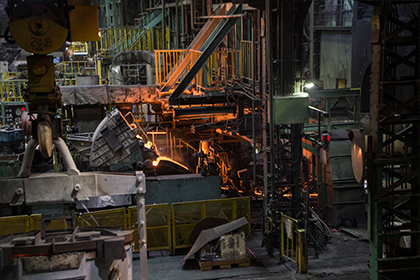
阪神工場武庫川事業所の鋳造ライン全景。
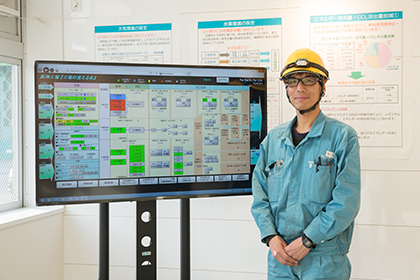
工場の可視化についてお聞きした、KPS推進課 足立誠さん。